Transforming Industrial Property Layouts for Maximum Efficiency
- Simon Lim
- Dec 3, 2024
- 3 min read
In today's fast-evolving industrial landscape, optimizing workflow is essential. A well-crafted layout can drastically improve productivity while cutting down costs. A smart design does more than look good. It ensures processes run smoothly, minimizes waste, and positively impacts the bottom line.
Let’s explore the crucial elements of effective industrial property layouts and discover how layout optimization can foster a more efficient operational environment.
Key Design Elements
Efficient Floor Plans to Maximize Usable Space
The foundation of any industrial facility is its floor plan. An effective layout maximizes space and boosts productivity. Utilizing open floor plans and strategically placing workstations promotes easy access and streamlined workflows.
For instance, consider a manufacturing facility where assembly stations are located near storage areas. This arrangement can cut material retrieval time by up to 30 percent, leading to quicker production cycles. By clearly defining zones—like assembly, storage, and maintenance—companies not only enhance efficiency but also create a safer work environment that keeps employees satisfied.
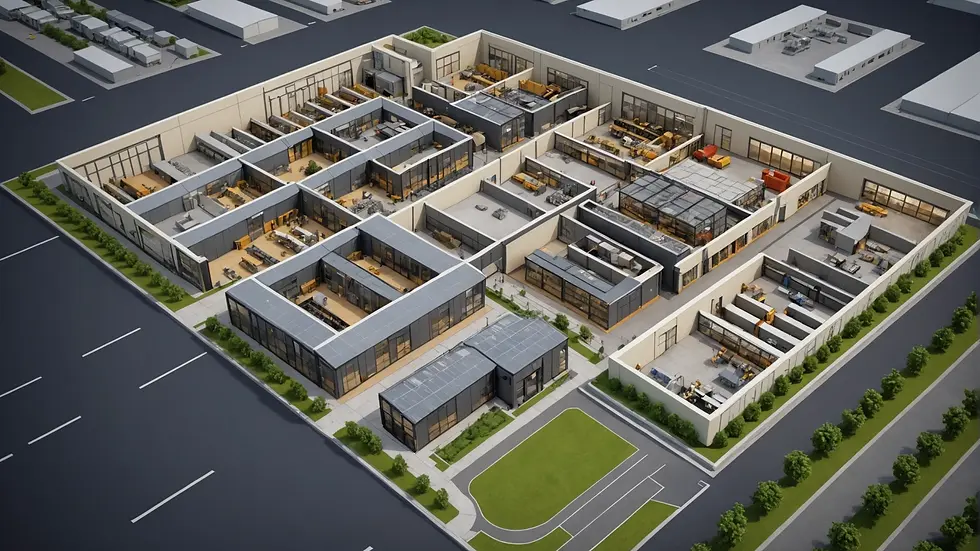
Strategic Placement of Loading Bays for Smooth Logistics
Loading bays play a critical role in industrial operations. Their thoughtful positioning can make or break logistics and supply chain processes. Placing loading docks close to storage areas reduces handling time—potentially decreasing it by around 25 percent—and streamlines the flow of inventory.
While planning the layout, consider factors like traffic flow, large vehicle accessibility, and the distance to entrances. Efficiently arranged loading bays minimize bottlenecks, enabling a smooth transfer of materials and products.
Importance of High Ceilings for Vertical Storage
High ceilings can significantly enhance how space is used in an industrial property. Vertical storage allows for increased capacity without cluttering the floor. Companies that implement shelving systems reaching 20 feet or higher can boost their storage capabilities by nearly 50 percent, all while keeping operations organized.
High ceilings also make room for automated systems like robotic retrieval systems. These technologies not only save time but also aid in maintaining an orderly and efficient workspace.
Technology Integration
Incorporating Automated Systems into Layouts
In an age where automation is taking center stage, integrating technology into industrial layouts is essential. Automated systems, including conveyor belts and robotics, can reduce labor costs and expedite production.
When planning the facility, it's crucial to think about how these technologies will fit within the layout. A design that allows easy access for maintenance helps ensure uninterrupted operations, ultimately benefiting output efficiency.
IoT-Enabled Layouts for Real-Time Tracking and Monitoring
The Internet of Things (IoT) is a game-changer for facility management. Incorporating IoT-enabled layouts means businesses can monitor equipment, materials, and workflows in real-time.
For example, using sensors throughout a warehouse can help a business track inventory levels continuously. If a product runs low, an alert can prompt restocking before it affects operations. This data-driven approach can improve overall facility efficiency by upwards of 30 percent, as operations can adapt in real-time to changing needs.
Customization for Industry Needs
Warehousing vs. Manufacturing: Tailored Design Considerations
Different industrial sectors present unique challenges in layout design. For example, warehousing focuses on maximizing storage space and efficient picking processes, whereas manufacturing often demands layouts conducive to smooth production lines.
Understanding these industry-specific needs is vital for creating layouts that enhance operational efficiency. Tailored designs that take into account the particular demands of each sector can lead to better resource management and improved overall functionality.
Cold Storage Facilities and Temperature-Controlled Layouts
Cold storage facilities are crucial in industries like food distribution and pharmaceuticals. Designing temperature-controlled layouts necessitates careful attention to insulation, refrigeration systems, and product flow.
An optimal layout will enable efficient movement of goods while keeping them in a temperature-sensitive environment. For instance, a food distribution center may require quick access to ensure products remain frozen during transfer, reducing temperature fluctuations. Designs that facilitate seamless entry and exit can decrease handling times by 20 percent, ensuring compliance with health regulations and improving product quality.
The Path Forward
Careful planning in layout design can transform industrial properties. By prioritizing optimization, companies can elevate productivity and significantly cut costs.
Every detail—from innovative floor plans to the strategic placement of loading bays and technology integration—contributes to the overall success. By focusing on these elements, businesses can unlock the hidden potential of their industrial spaces, laying the foundation for growth and efficiency.
In a competitive market, leaders who embrace layout optimization put themselves in a strong position to address future demands effectively. Sustainable growth starts with a robust foundation: an efficient and well-considered industrial layout.
Simon Lim
+6016-448 9663
Comentários